VPI (Vacuum Pressure Impregnation) System
AEM is proud to announce the installation and commissioning of a new VPI (Vacuum Pressure Impregnation) system. This new addition does not only enhance AEM’s capability but also improves our services to the customers by ensuring increased reliability and maximized performance of the windings systems of high and low voltage motors, generators, and other electrical equipment.
What is Vacuum Pressure Impregnation?
Vacuum Pressure Impregnation (VPI) is basically an impregnating process for the rewound components (e.g. stator, rotor, armature windings). As its name suggests, it entails vacuum and pressure cycles during the impregnation stage.
The VPI process removes moisture and air voids from the winding insulation by first applying a vacuum, then introducing resin under vacuum, and finally applying high pressures to push the resin into the pockets and crevices of the winding insulation materials.
For a successful VPI process, it is imperative to have a strong control of timing, vacuum/pressures, and the temperatures along with the use of high-quality insulation materials/resin.
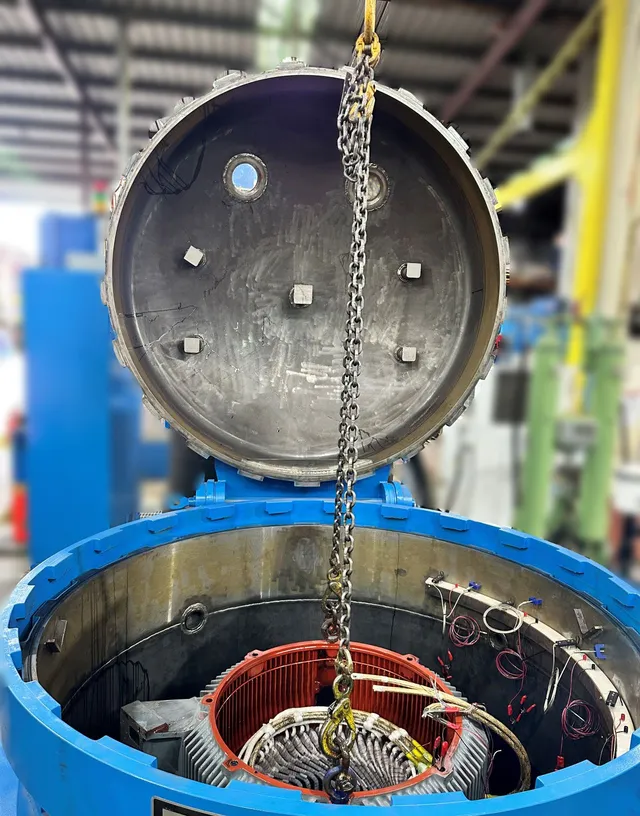
Benefits of VPI
A winding that is properly VPI processed and baked will have superior characteristics, which will support a longer insulation life, greater heat dissipation and hence, reduced probability of motor failure. Some of the key benefits are:
- Enhanced dielectric (insulation) strength
- Excellent heat transfer
- Better performance in harsh environment and superior protection against the contaminants
- Enhanced mechanical strength